In today's competitive marketplace, understanding the cost dynamics of Reformers is crucial, especially for companies looking to invest in this essential technology. Reformers are intricately designed devices, critical for industries like petrochemical, energy, and even pharmaceutical sectors, as they play a pivotal role in gas production, primarily hydrogen.
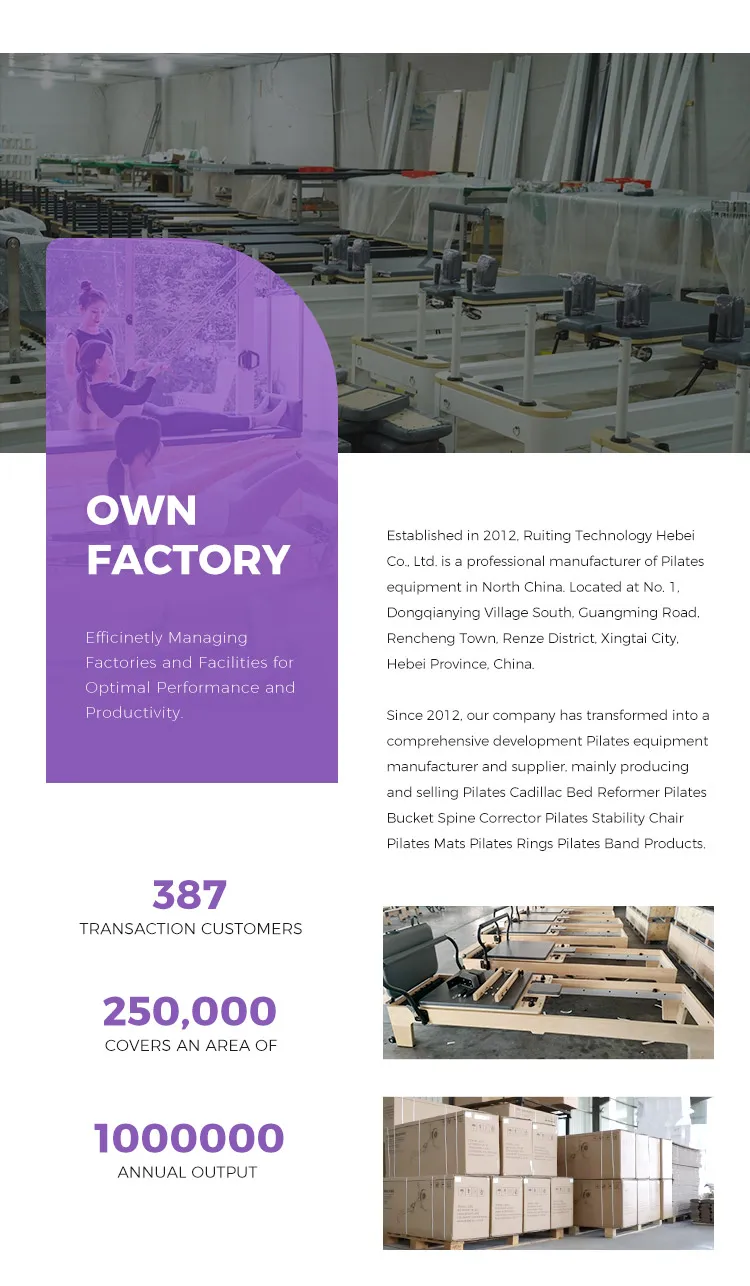
Understanding Reformer Cost Components
Reformer costs are multifaceted and hinge on several critical factors. Firstly,
the type of reformer plays a significant role. Steam methane reformers (SMR), autothermal reformers (ATR), and partial oxidation reformers (POx) each have unique technological underpinnings, influencing the overall expenditure. SMRs, the most widely used, often incur costs related to the complex heat exchanger units and intricate catalyst layers necessary for the methane conversion process.
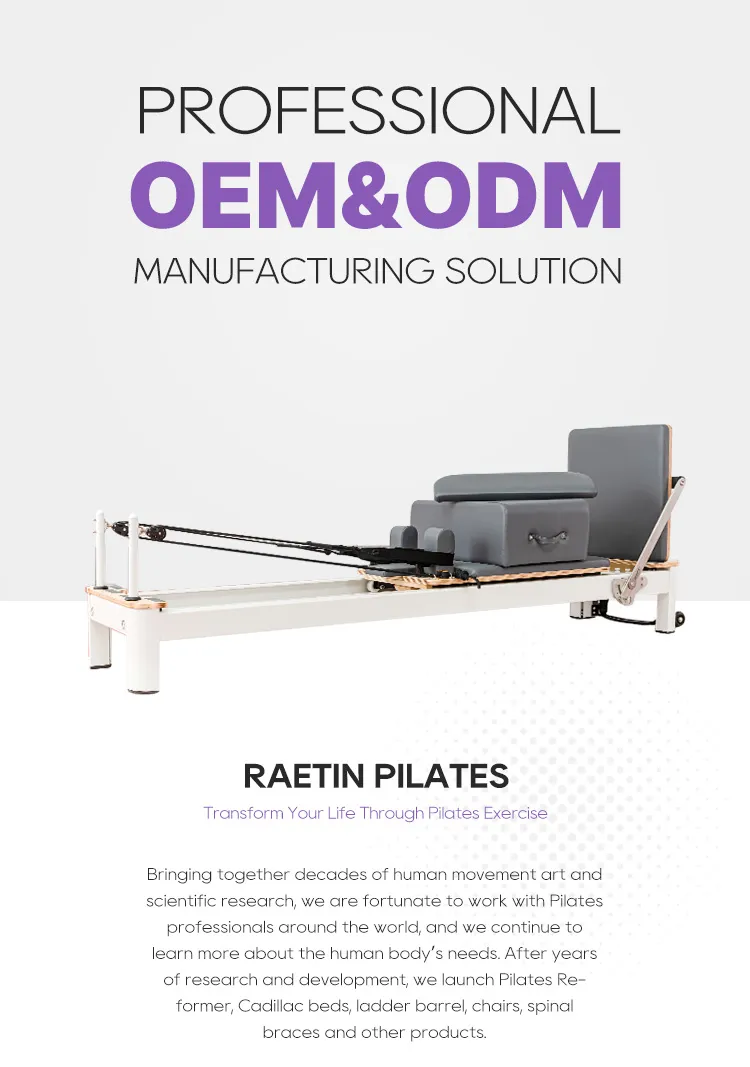
Material selection is critical. High-temperature and pressure-resistant alloys are prerequisites for construction, alongside ceramic and composite materials which withstand the harsh operational environment. These material choices significantly impact the procurement budget.
Operating Costs and Maintenance
Beyond initial procurement, operating costs are substantial. Reformers demand continuous, energy-intensive processes, primarily driven by natural gas, which is a fundamental cost component. Energy consumption across operating cycles is a significant determinant of the life-cycle cost of a reformer.
Maintenance, a pivotal aspect, involves periodic catalyst regeneration or replacement. The catalysts, often precious metals, require precise handling and careful recycling strategies to ensure cost efficiency and sustainability. Furthermore, routine inspections and repairs due to thermal cycling and material fatigue are unavoidable, adding to operational expenses.
Additionally, the expertise and training required for optimal operation should be factored into the equation. A well-trained workforce ensures that the reformer operates at peak efficiency, reducing unplanned downtimes and associated costs.
Investment in Technology and Innovation
reformer cost
Technological advancements significantly influence reformer costs. Investments in cutting-edge catalysts, innovative reactor designs, and digital monitoring systems are transforming traditional cost structures. Modern reformers equipped with advanced IoT sensors provide real-time data, allowing for predictive maintenance and reducing unexpected failures.
Furthermore, adopting green technologies and integrating carbon capture and storage systems (CCS) can offset operational costs by improving efficiency and meeting regulatory standards. Companies investing in these technologies stand to benefit from both reduced environmental impact and long-term cost savings.
Navigating Regulatory Landscapes
Navigating the complex regulatory requirements associated with reformer operation involves costs that extend beyond mere compliance. Companies must engage with expert consultants to ensure that installations adhere to environmental standards, safety regulations, and industrial codes. These compliance costs, although not immediately obvious, are essential for sustainable operations.
Strategic Cost Management
A robust strategic approach to cost management can ensure optimal returns on investment. This includes negotiating favorable terms with suppliers, leveraging bulk purchasing agreements for materials, and collaborating with industry leaders for technological advancements. Moreover, implementing energy efficiency measures can significantly reduce ongoing costs, aligning operational strategies with broader sustainability goals.
Conclusion
Reformer cost considerations encompass a broad spectrum, from initial construction and materials to ongoing operational expenditures and regulatory compliance. Companies that strategically navigate these expenses by integrating technological innovations, maintaining a skillful workforce, and aligning with regulatory frameworks will enhance their competitive edge and operational efficiency.
For investors, financial analysts, and industry managers, understanding the intricate dynamics of reformer costs is crucial. It ensures that the substantial financial outlay required for these pivotal devices translates into productive, efficient, and sustainable industrial operations.