Navigating the intricate dynamics of reformer technology, especially considering its cost, demands a comprehensive understanding bolstered by both real-world experience and technical expertise. Reformer systems, predominantly used in industries like chemical manufacturing and energy production, play a critical role in transforming hydrocarbons into hydrogen-rich fuels. The cost considerations surrounding these systems are not merely financial but span efficiency, longevity, and environmental compliance.
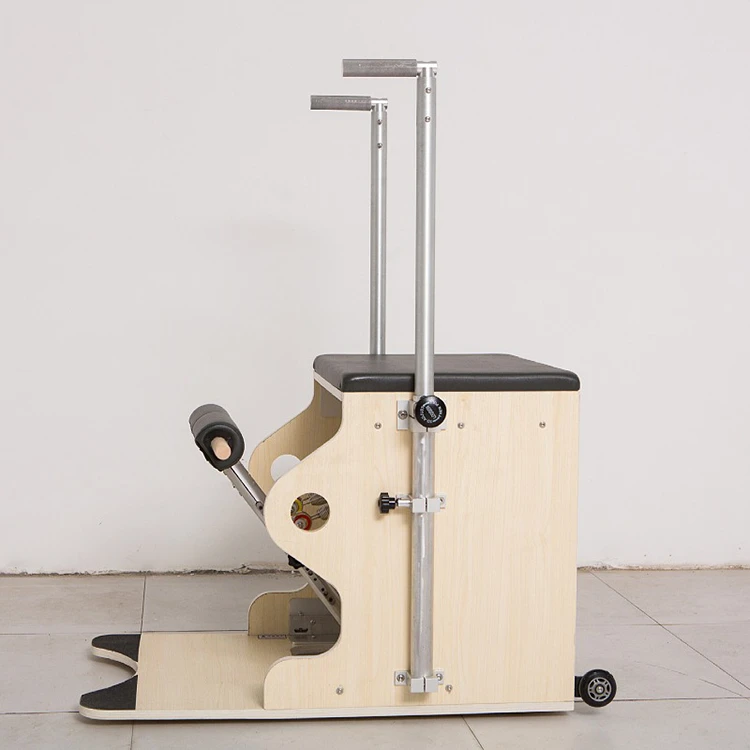
A fundamental component in evaluating the cost is the type of reformer. Steam Methane Reformers (SMR), Partial Oxidation Reformers (POX), and Autothermal Reformers (ATR) each come with distinct operational mechanics and cost implications. For instance, SMRs are renowned for their high efficiency in hydrogen production but demand significant capital investment and rigorous maintenance schedules. Conversely, POX entails lower upfront costs but might incur higher operational expenses due to its energy intensity.
In interviewing industry veterans, a recurrent theme emerges the cost-effectiveness of a reformer is significantly influenced by the end-use application and the scale of operation. Large refineries, capitalizing on economies of scale, often find that investing in SMR units is financially advantageous over the long term. In contrast, smaller operations might opt for ATR due to its flexibility in handling feedstock variations and lower initial costs.
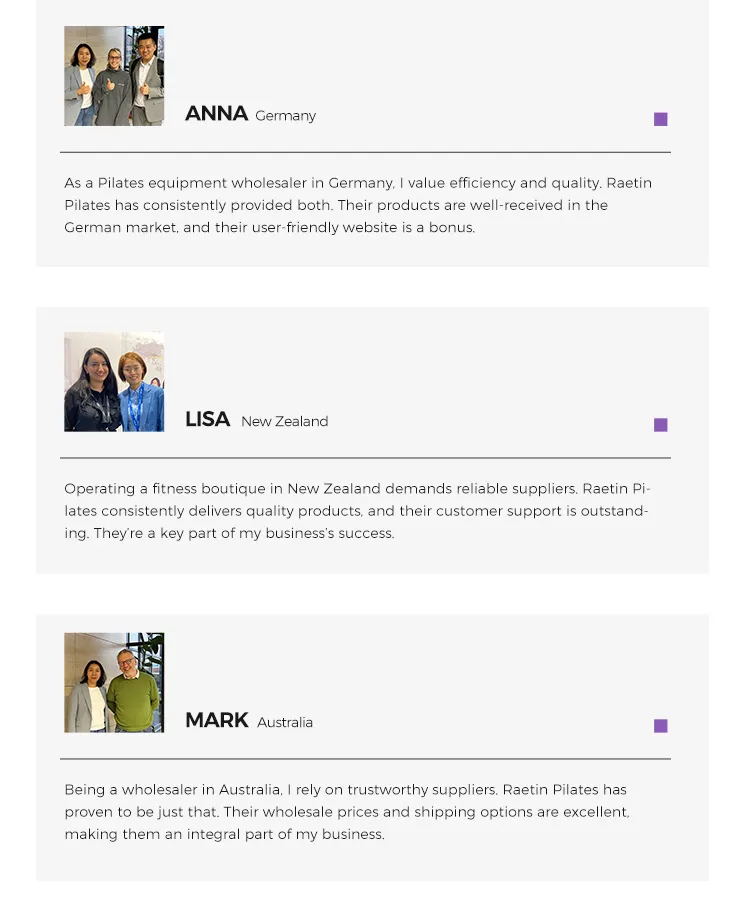
Authoritative insights from industry reports suggest that the design optimization of reformers, encompassing both catalyst efficiency and heat recovery systems, plays a pivotal role in managing long-term operational costs. For instance, advanced catalyst technologies have been pivotal in reducing carbon emissions and extending the lifespan of reformers, subsequently lowering environmental compliance costs and extending operational viability.
cost of reformer
Trust, in this context, is built on a track record of successful deployments and operational transparency. Manufacturers who provide detailed lifecycle analyses and case studies help companies make informed decisions by projecting accurate cost vs. value scenarios. A reformer's Total Cost of Ownership (TCO), which includes installation, operation, and decommissioning costs, is a critical metric for businesses aiming to align their operational strategies with fiscal prudence and sustainability goals.
Conversations with plant managers highlight another layer of cost consideration energy efficiency. Energy consumption is often the largest ongoing expense in reformer operations. Thus, reformers that integrate cutting-edge technologies like heat exchangers or digital monitoring systems can significantly reduce energy bills. These innovations not only optimize the reforming process but also enhance the reliability and safety of the operation, reducing downtime and maintenance costs.
In conclusion, the cost of reformers cannot be encapsulated by a single price tag. It embodies a multifaceted assessment of technology type, operational scale, energy dynamics, and future-proofing capabilities. Decision-makers in this realm must weigh their objectives against these varied factors, ensuring that their investment not only meets current production needs but also aligns with future growth and sustainability targets. With the right balance, reformer systems can yield considerable operational advantages, paving the way for enhanced efficiency and profitability in the industrial landscape.